AIT Supports Multimillion-Dollar Temperature-Controlled Pharmaceutical Launch with Flawlessly Executed Cold Chain Plan
Published on: Jun 26, 2019
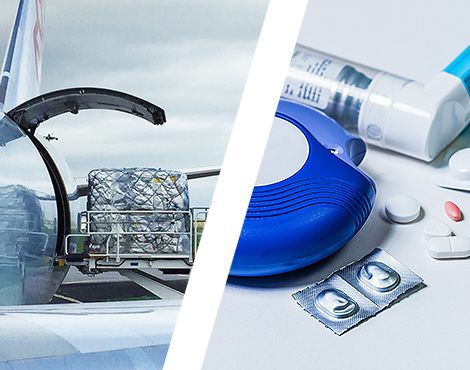
The Challenge
In preparation for the launch of a new drug in the United States, a global pharmaceutical company turned to their trusted supply chain partner, AIT Worldwide Logistics, to orchestrate a move. The drug manufacturer had been building a stockpile of the respiratory management medication at their facility in Dublin, Ireland while awaiting final approval from the Federal Drug Administration (FDA) in the United States. With the approval process nearing a conclusion, AIT initiated the transfer of the launch inventory (320 temperature-controlled pallets valued at approximately $4.5 million) to the pharmaceutical company’s U.S. distribution center.
Timing, security and stability are always high priorities when shipping finished pharmaceuticals, but these aspects become hyper-critical when bringing a new product to market. AIT’s Life Sciences team spent months in advance planning for this moment and they were prepared to execute immediately.
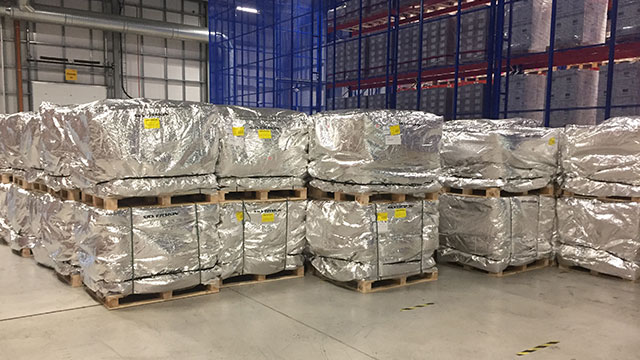
The Solution
The process began with finalizing equipment and personnel. AIT’s operations experts chartered a temperature-controlled 747 freighter aircraft to haul the entire stockpile on a single AIT-controlled flight while maintaining a constant 20° C. Since the product was still awaiting final FDA approval, the only way to bring it into the U.S. was under the FDA’s Pre-Launch Activities Importation Request (PLAIR) program which requires the entire launch inventory to arrive as a single shipment. Next, two fleets of refrigerated trailers with drivers and security teams were arranged – one group in Ireland; another in the U.S. Finally, AIT worked with the origin and destination airports in Ireland and the U.S. to schedule supplemental teams of ground personnel dedicated solely to this project.The process began at the drug manufacturer’s temperature-controlled facility in Dublin where seven refrigerated trailers arrived on a Wednesday evening. Over the next several hours, each trailer was loaded with 40 to 50 pallets while maintaining a constant temperature between 15° and 25° C. As a safeguard, AIT hired a team of refrigerated service technicians to spend the evening on-site with tools and parts at the ready in the unlikely event of a mechanical failure.
For every trailer-load, multiple active GPS tracking units were affixed to the outside of the pallets. These redundant devices continuously monitored the cargo from the time it was first loaded in Ireland until final delivery in the U.S. Knowing the sensitive nature of the high-value cargo, AIT’s Life Sciences experts proactively provided the drug manufacturer’s security team with location and temperature updates every 30 minutes throughout the lifecycle of the shipment.
The refrigerated trailers remained at the facility until early the next morning when they began their runs to Shannon Airport on the west coast of Ireland. As a security precaution, chase cars were hired to accompany the trucks on the 200+ kilometer drive. Departures from the facility were staggered so that the trucks arrived at the airport one-by-one. With each arrival, the supplemental ground crew unloaded and screened the pallets, finishing one trailer-load just as the next truck was pulling in.
The finished pharmaceuticals had been packaged in insulated boxes and the pallets were wrapped in silvery passive thermal covers. Despite these effective temperature-maintenance measures, minimizing dwell time (i.e. time cargo spends in an area that isn’t temperature-controlled such as a loading dock) was still a priority for the team. The staggered arrivals of the trucks at Shannon Airport kept the cargo moving once it was unloaded. With the extra personnel on hand, security screening took place immediately. Bundles of five to ten screened pallets were consolidated onto Unit Loading Devices (ULDs) which made loading the airplane more efficient. The pallets were plastic-wrapped to protect from adverse weather and encased in netting on the ULDs.
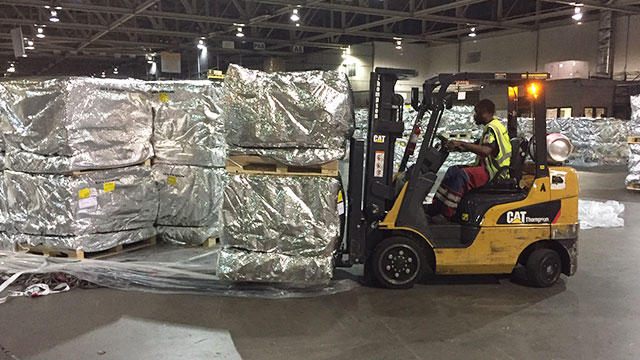
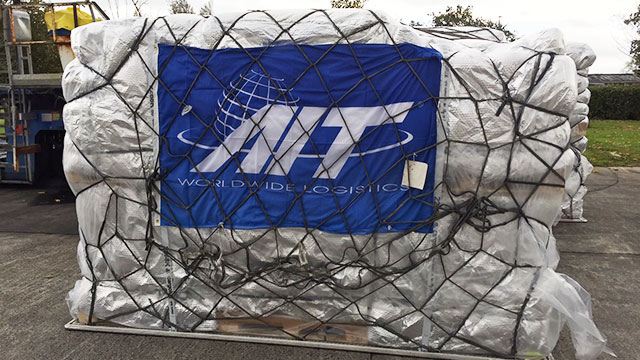
Just as the final ULD build-up was being completed, the charter aircraft arrived at Shannon Airport. Utilizing 34 positions on both the main and lower decks of the aircraft, the dedicated ground crew had all the ULDs fully loaded by mid-afternoon. The flight plan was filed and the 747 freighter took off in the early evening with an AIT’s Director of Life Sciences on board to personally monitor the cargo.
While the plane was in the air, AIT’s Customs Brokerage team cleared the entire shipment of finished pharmaceuticals with U.S. Customs by utilizing the “wheels up” program. Eight hours later, the flight arrived at Hartsfield-Jackson Atlanta International Airport with the cargo ready to be off-loaded immediately thanks to the in-flight clearance.
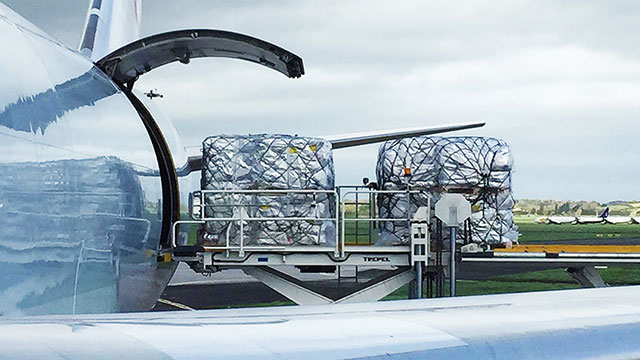
Despite the chartered 747 arriving well into the nighttime hours, there were plenty of dedicated ground personnel available per AIT’s action plan. The ground crew were joined by a teammate from AIT-Atlanta’s office and a representative from the pharmaceutical company to oversee the final stages of the operation. The 34 ULDs were off-loaded from the plane, broken down into individual pallets and loaded onto a fleet of trucks for staggered delivery to the drug manufacturer’s cold storage facility in North Carolina.
The Result
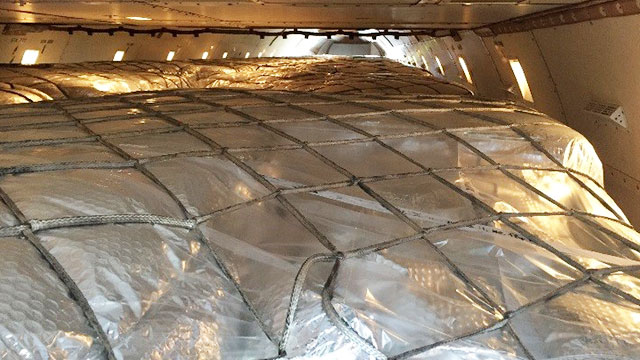
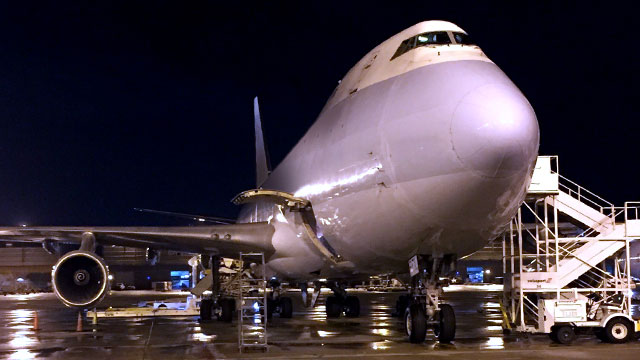
Meticulous planning by AIT’s Life Sciences team resulted in a perfectly executed project. They minimized dwell times by staggering departures for the refrigerated trucks and arranging for dedicated ground personnel crews at both airports. The team also chartered a single 747 aircraft to keep all 320 pallets of finished pharmaceuticals together under a PLAIR with the FDA. Utilizing the “wheels up” program, AIT’s Customs Brokerage team cleared the goods while they were in the air which saved hours upon arrival in the U.S. Finally, GPS tracking technology provided pharmaceutical company representatives with accurate location and temperature data at their fingertips throughout the shipment’s lifecycle.
Successfully positioning the product at the U.S. facility meant that the drug manufacturer was poised to launch immediately once final FDA approval was obtained. Since the initial launch, the pharmaceutical company has relied on AIT to establish and maintain an inventory replenishment supply chain from Dublin to North Carolina.
In the four months following the product launch, AIT’s Life Sciences team has delivered more than 2,000 pallets of finished temperature-controlled pharmaceuticals utilizing scheduled commercial carriers. Thanks to AIT’s operational prowess, these shipments have been successfully trucked from Dublin to the drug manufacturer’s U.S. distribution center with a consistent door-to-door transit time of less than 36 hours and zero temperature excursions.