AIT's Food Logistics Team Helps Global Restaurant Chain Preserve Its Brand Integrity
Published on: Jan 30, 2019
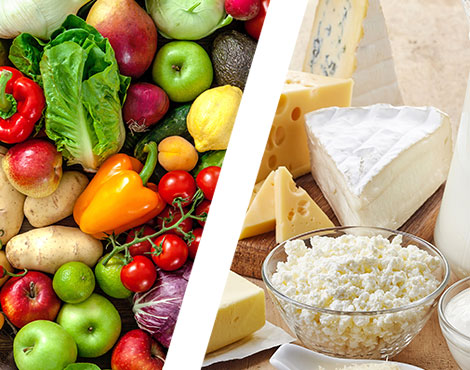
The Challenge
A global fast-food restaurant chain with franchise locations around the world wanted to improve the reverse logistics operations that support their ongoing quality control process. Consistency and quality is of paramount importance since the fast-food giant is committed to delivering the same recognizable product for consumers whether they visit a location in Kansas City or the United Arab Emirates. Dependably providing a high-quality final product begins with high-quality ingredients which must be sourced locally to control costs.To ensure consistent quality for their brand, the restaurant chain’s corporate office in the United States regularly receives ingredient samples shipped from a variety of international locations in Asia, Europe, Oceania, the Middle East and South America. However, most of the local businesses supplying bakery, dairy, produce and protein ingredients in these regions are smaller companies that do not have experience exporting their products. Using one of the large integrators to ship samples is not a sustainable option. The integrators do not provide one-on-one guidance to help shippers and customers accurately prepare the required import and export documentation, nor do they offer packing services for fresh and frozen samples that can maintain cold chain integrity for the duration of an international journey.
The Solution
Unlike most companies that provide transportation and supply chain management, AIT Worldwide Logistics develops full-service solutions that meet the door-to-door needs of its customers all over the world. The professionals on AIT’s Food Logistics team apply decades of cold chain expertise to make sure that every individual link in the supply chain is carefully planned and diligently executed.In meeting this challenge, AIT team members reach out to suppliers in locations such as Australia, Brazil and India to gather information about the food samples that need to be shipped to the customer’s global headquarters in the United States. After gaining an understanding of the product and temperature requirements, the team applies their existing internal operating procedures to handle the various foodstuffs being shipped. Once samples have been picked up from the suppliers, AIT handles all the packing using specially-designed shipping materials to maintain temperature integrity. AIT then completes the door-to-door service with expedited air transport and final delivery at the customer’s corporate destination.
Shipping food internationally can generate overwhelming regulatory paperwork, but AIT’s team members are experts when it comes to navigating governmental hurdles. For example, the team provides line-by-line guidance for customers when they are applying for import permits with controlling agencies including the Food and Drug Administration and the Department of Agriculture’s Food Safety and Inspection Service. With AIT’s expert assistance, the process of importing the samples into the U.S. is fully compliant with these agencies’ regulations. Likewise, the Food Logistics team works closely with their counterparts on AIT’s Customs Brokerage team to take advantage of wheels-up clearance that allows for rapid transfer to ground transportation once the shipments arrive in the U.S.
The Result
With diehard attention to detail, AIT’s team successfully delivers refrigerated and frozen samples to the restaurant chain’s corporate office in the United States on an ongoing basis. Product integrity and cold chain consistency is maintained throughout the process thanks to stringent packing and shipping procedures that preserve the required temperatures. The samples also arrive on-time since the team avoids delays by diligently assisting with preparations for all regulatory requirements including import permits and customs clearances. When the occasional delay caused by an unpredictable event such as bad weather occurs, the team is well-prepared to respond and maintain cold chain consistency with worldwide resources including re-packaging and re-icing capabilities.Coordinating the deliveries of the samples to arrive in a pre-determined timeframe allows the customer’s quality assurance group to test the ingredients in their controlled environment at the corporate office rather than traveling around the world to conduct product evaluations. With AIT’s Food Logistics team handling the fine details to eliminate temperature excursions while shipments are in transit, the customer is free to focus on in-house quality testing to confirm that ingredients supplied by local companies are continuing to meet the standards of the brand. As a result, the customer’s brand integrity is preserved and transportation costs are minimized with the ongoing sourcing of high-quality local ingredients for their global restaurant locations.