Multi-Stop Trucking Solution Minimizes Damages, Maximizes Efficiency for Big Box Retailer Rollout
Published on: May 22, 2019
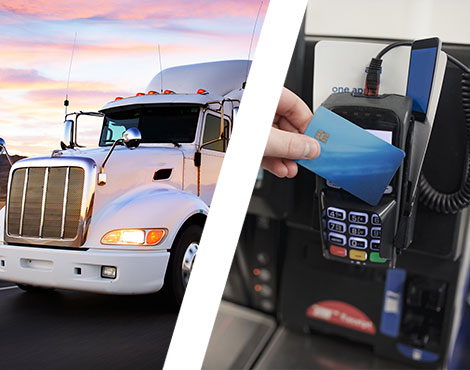
The Challenge
One of the largest big box retailers in the United States was in the process of modernizing their checkout lanes by installing self-checkout systems in new and existing stores across the eastern United States. The retailer placed an order for more than 200 units which were staged in a central distribution location in preparation for the rollout to stores.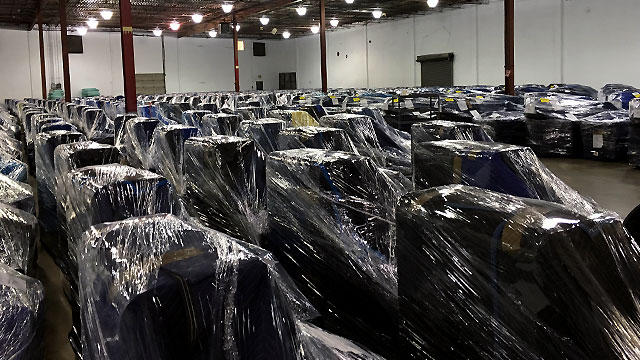
Traditionally, a Less-Than-Truckload (LTL) solution would be used for a Point-of-Sale (POS) rollout of this magnitude. But the bulky self-checkout systems weighed in at more than 750 pounds each and the manufacturer knew from experience that the typical LTL approach carried a greater risk of damage to the units. They also knew that AIT’s Retail Logistics team provided a solution that was proven to be superior.
The manufacturer passed along a recommendation to the retailer suggesting that they use AIT for the rollout. When representatives from the retailer met with retail logistics experts from AIT to discuss the project, AIT’s prowess with handling self-checkout systems was immediately apparent. Moreover, by asking insightful questions, the AIT team members demonstrated their commitment to a well-defined distribution and installation process that would meet the retailer’s end-to-end needs.
The Solution
Taking the manufacturer’s advice to heart, the retailer gave AIT the opportunity to manage the rollout and earn their trust. Each week, a list of stores (sometimes 12 or more) and delivery dates was submitted to the project control tower at the AIT-Memphis office. Utilizing a multi-stop full truckload model, subject matter experts created routing for each week’s deliveries while considering multiple variables including store location and hours, installer availability, weather forecasts and more.The final routings involved loading units for as many as six stores per truckload oftentimes with destinations in multiple states. Self-checkout systems for locations that were last on the schedule were nose-loaded into the 53-foot trailers while the units earmarked for delivery at the first stop were tail-loaded. The multi-stop trucking solution greatly minimized the number of times the units were loaded and unloaded which in turn minimized the risk of damage to the units.
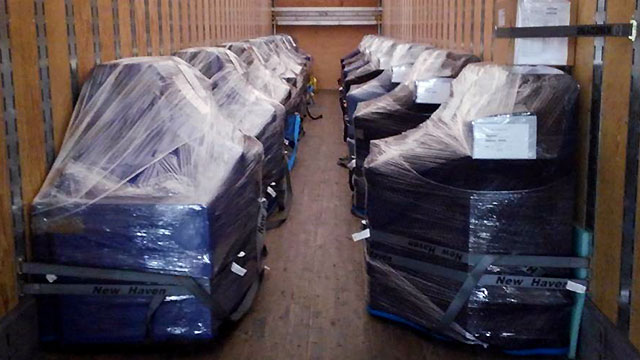
Given that the self-checkout systems exceeded six feet in length and five feet in height, all parties agreed that crating the individual units would be prohibitively expensive. Despite their bulk, the systems were still delicate and required white glove handling. AIT provided pads, load straps and foam spacers, but the team also developed standard operating procedures with strict carrier equipment requirements including highly specific guidelines for the environment inside the trailers.
Given the nature of the retail business, all deliveries were scheduled late at night (9pm local time or later) to avoid disrupting normal business hours with many of the installations slated for weekends. The AIT-Memphis control tower took special care to prepare representatives from the individual store locations with proactive communication about what to expect when the trucks arrived with the self-checkout systems. Likewise, coordination took place with local installation professionals so their late-night arrival coincided simultaneously with AIT’s two-person delivery teams. Timing was a critical factor: an early arrival while the store was still open would be just as detrimental as a late delivery.
At the retailer’s corporate office, representatives monitored the rollout over the course of several months using a customized online portal that presented complete shipment visibility. On-demand tracking provided 24/7 real-time updates while pre-programmed geo-fence notifications alerted the retailer when units were arriving at a location for installation.
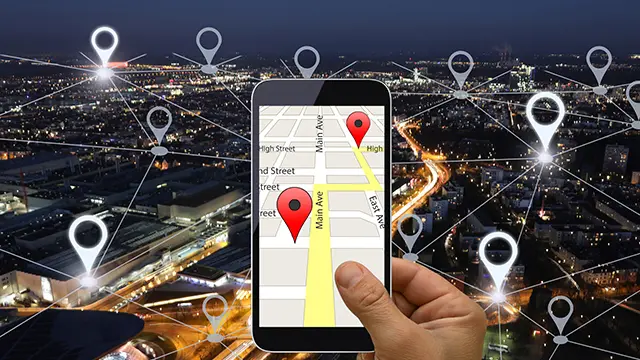
The Result
AIT’s comprehensive managed solution for the rollout resulted in 200+ self-checkout systems being successfully delivered and installed at store locations in 16 states over the course of several months. By applying a multi-stop trucking model with meticulous routing, AIT’s retail logistics experts provided efficient, cost-effective delivery while minimizing the risk of damage to the units.
Encouraged by AIT’s performance with the rollout, the big box retailer dramatically expanded the partnership between the two companies. AIT’s Residential Delivery team is now delivering furniture sold by the retailer directly to consumers’ homes. Meanwhile, the Retail Logistics team is handling a new shopping cart rollout as well as palletized business-to-business shipments to local shops buying bulk goods from the retailer for resale.
Encouraged by AIT’s performance with the rollout, the big box retailer dramatically expanded the partnership between the two companies. AIT’s Residential Delivery team is now delivering furniture sold by the retailer directly to consumers’ homes. Meanwhile, the Retail Logistics team is handling a new shopping cart rollout as well as palletized business-to-business shipments to local shops buying bulk goods from the retailer for resale.
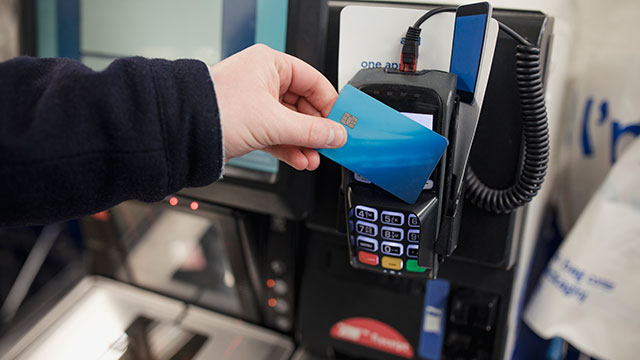
More than 200 self-checkout systems were delivered and installed in store locations across 16 states
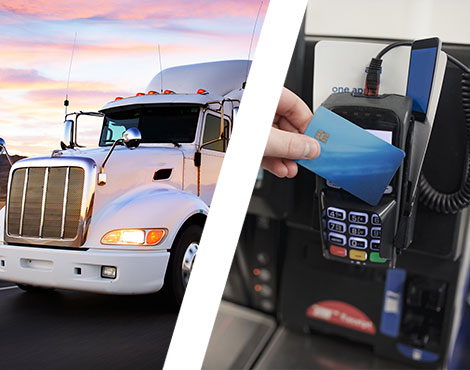